Recombinant Insulin
Cell culture in bioprocessing
Cell culture remains one of the most important bioprocessing tools we have today.
Cell culture remains one of the most important bioprocessing tools we have today
Biotherapeutics production largely depends on cell culture, the process of growing cells under tightly controlled artificial conditions with the scope of producing a large amount of the desired therapeutic protein. The classic example of this process is cell culture of a Chinese hamster ovary (CHO) cell line, used to express therapeutic proteins such as antibodies, cytokines, enzymes, and hormones.
Cell culture methods are also instrumental in the development and propagation of many types of viruses, which can be used in viral vaccines and as a delivery mechanism for gene therapies. Another growing application is stem cells therapies, which hold great potential for regenerative medicines and which must be expanded and propagated through a careful cell culture process.
Despite the technique first being developed by Ross Harrison in 1907, cell culture remains one of the most important bioprocessing tools we have today. High production yields are the primary sign of a successful upstream bioprocess, therefore the critical importance of a fully optimised cell culture process cannot be underestimated.
Cell culture media: Moving from classical to serum-free
By the early 1950s, researchers had determined that cell growth depended on a basal mix of salts, sugars, amino acids, and vitamins, plus a supplement of poorly defined biological fluids or extracts of plasma or serum from animal sources. This mix became known as cell culture media – the all-important source of nutrients needed for cells to survive and proliferate.
While the growth factors and hormones provided by the animal plasma or serum were considered essential requirements for cell proliferation, the use of fluids from animal origins presented some limitations, namely a lack of consistency and a risk of infection.
In the 60s and 70s, many scientists were working to develop chemically defined, serum-free media that could offer greater safety, consistency and performance while also overcoming the ethical concerns associated with the use of animal components. Without the serum or plasma, however, such media had the limitation of lower product yields due to reduced cell proliferation.
To overcome this, researchers tested a range of ‘synthetic’ (or recombinant) supplements such as growth factors, hormones, albumin, and transferrin. An important discovery was published by Gordon H Sato and David Barnes in 1980, who had found one particular growth factor, insulin, “to be stimulatory in serum-free media for the growth of virtually every cell type examined”.[1]
[1] 14. Barnes D and Sato G. Serum-free culture: a unifying approach. Cell22:649-655 (1980).
Recombinant Insulin for serum-free media
Today, the cell culture world is still divided into classical and serum-free solutions, but the industry is increasingly turning towards serum-free options. The increased research and development around advanced therapies based on stem cells and chimeric antigen receptor T-cells (CAR-T cells) is driving this movement, as these therapeutics require carefully balanced culture conditions and specialised cell culture media.
While there are many commercial cell culture media options available, many companies choose to develop their own custom formulation to achieve their desired bioproduction metrics. Recombinant insulin is a go-to supplement for serum-free media and is frequently used in CHO-s, HEK 293, and Sf9 cell lines in the manufacture of monoclonal antibodies, virus vaccines, and gene therapy products.
Novo Nordisk Pharmatech is the leading supplier of Recombinant Insulin for bioprocessing applications. Produced by microbial expression in yeast, our Insulin Human AF product is used by many of the world’s leading biopharmaceutical companies to stimulate cell proliferation and enhance production yields. This allows companies to decrease the amount of cell culture media they use in bioprocessing.
The quality of our insulin, which is sourced directly from our parent company, Novo Nordisk—the world’s largest producer of therapeutic insulin—guarantees a pure and consistent product. No animal components are used in the cell bank and manufacturing process, and the yeast organism used for production contains no genes or expresses antigens of livestock or disease agents.
The product is manufactured under ISO 9001 Quality Systems and cGMP compliance and fulfils all relevant European and US guidelines and pharmacopoeia, making it fully safe to use in cell culture systems for innovative biologic therapies.
Explore more
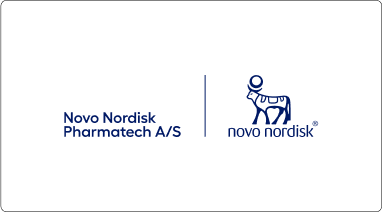
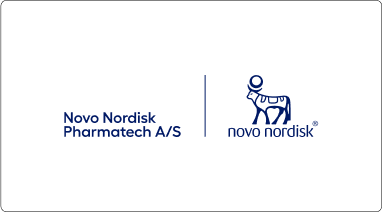
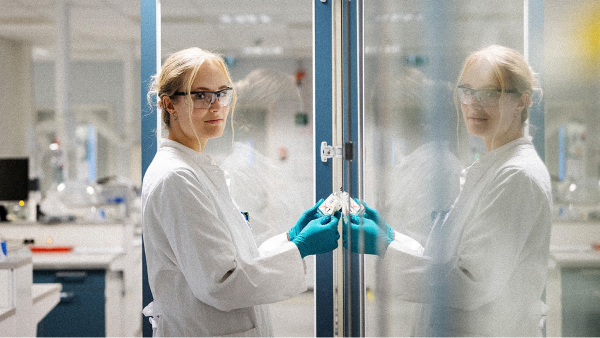
Valuechain
Novo Nordisk Pharmatech improves biopharmaceutical manufacturing by developing and supplying innovative products used in the manufacturing of biopharmaceuticals.
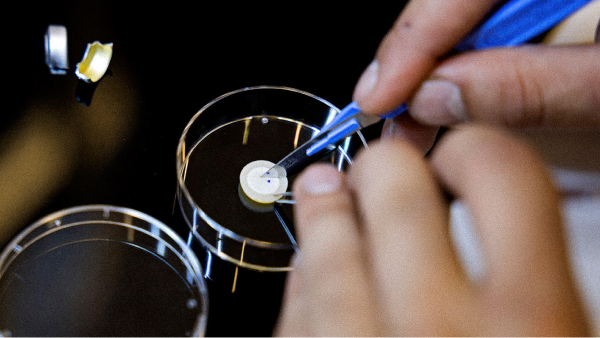