Solutions
Recombinant Insulin FAQ
Our high quality Recombinant Insulin
What is Recombinant Insulin?
Recombinant Insulin, also known as Insulin Human AF, consists of human insulin crystals, a biosynthetic white powder produced by a recombinant microbial expression in yeast with a synthetic gene insert.
Press the link to watch the video.
Is your Recombinant Insulin animal free?
Our Recombinant Insulin aligns with the definition of an animal-free product from major cell culture media suppliers. The cell bank and manufacturing process do not involve any animal-origin components. The yeast organism used for production does not contain genes or express antigens of livestock or disease agents. The trypsin used in the process is substituted with a proprietary process aid of non-animal origin. Furthermore, our insulin is free of antibiotics, both in production facilities and at the cell bank level.
What applications is your Recombinant Insulin suitable for?
Recombinant Insulin is a key component in serum-free cell culture media for mammalian cells. It is used for the manufacturing of monoclonal antibodies, cell-based vaccines, viral vector-based gene therapy, and cell therapy. Recombinant Insulin stimulates the proliferation of cells and enhances the yield.
You can learn more about the applications here.
How do you ensure the quality, purity and consistency of your Recombinant Insulin?
Our Recombinant Insulin, produced by our parent company, Novo Nordisk, a leading insulin supplier for over a century, is the same high-quality insulin used worldwide for therapeutic purposes. It is manufactured in cGMP facilities, adhering to an ISO 9001 quality system. Our highly standardized processes ensure consistent product quality. The insulin is analyzed in accordance with the current European Pharmacopoeia (Ph. Eur.) and the United States Pharmacopoeia (USP). Both Novo Nordisk and Novo Nordisk Pharmatech are routinely audited by pharmaceutical companies, as well as health authorities.
How can you support customers during regulatory approval?
We offer a straightforward, all-in-one approach to regulatory compliance, delivering everything you require quickly and conveniently. We provide ongoing support for your inquiries and requests well beyond supplier qualification and delivery, throughout your entire product life cycle. Customized to meet your service needs, our comprehensive documentation and support package encompasses:
- ISO 9001 Certificate
- Certificate of Analysis (current Ph. Eur. and USP pharmacopoeias)
- Customer audits
- Quality agreements
- Declarations and statements (stability, residual solvents, TSE/BSE, GMO, allergens, etc.)
- Change Notification
- Answering of questionnaires
- Process flowchart
- Packaging details
- SDS
How do you ensure safe delivery and security of supply?
Offered in packing sizes ranging from 1 g to 1 Kg, our Recombinant Insulin is filled within our proprietary classified room facilities.
The product is dispensed into various HDPE plastic containers, each placed in a tamper-proof plastic bag. These tamper-proof containers are then packed in approved thermo containers, within a cardboard box and accompanied by dry ice to maintain the product below the recommended maximum temperature during shipment.
We maintain a stocked inventory of Recombinant Insulin for at least five months of consumption, allowing us to address your specific needs promptly.
Our Recombinant Insulin has a shelf life of five years. With two strategically located distribution centers near Copenhagen, Denmark, and in Indiana, USA, we ensure rapid delivery and precision shipping worldwide.
I am using CHO (HEK293, BHK…) for protein expression. What insulin concentration do you recommend adding to the base medium to improve growth or expression?
We recommend a titration of various insulin concentrations (from 1 mg/L to 20 mg/L) with your cell line and medium in a small batch culture to find the optimal insulin concentration for your conditions. You can then evaluate if insulin addition during cell growth (e.g. day 0, day 3, day 6) further improves growth, viability or productivity.
How can Recombinant Insulin help improve process efficiency during manufacturing?
Recombinant insulin is used in biomanufacturing processes to enhance yields by stimulating cell proliferation and cell productivity, resulting in increased production with greater efficiency.
Our studies have demonstrated notable improvements in yields. For instance, insulin has substantially augmented mAb production in CHO-K1 cells, achieving product yields of 6g/L. Furthermore, when applied to cell cultures of HEK-293 cells, insulin supplementation has been shown to enhance Influenza virus production by 51% for vaccine preparations. Our testing also revealed an increase in the production of both AAV and LV viral vectors.
For a comprehensive collection of available application notes on insulin usage, please refer to the “Insulin Application” page.
The incorporation of Recombinant Insulin into biomanufacturing processes enhances yields by stimulating cell proliferation and elevating cell productivity, ultimately aiding manufacturers in achieving their production targets with greater efficiency.
Our studies have demonstrated notable improvements in yields. For instance, insulin has substantially augmented mAb production in CHO-K1 cells, achieving product yields of 6g/L. Furthermore, when applied to cell cultures of HEK-293 cells, insulin supplementation has been shown to enhance Influenza virus production by 51% for vaccine preparations. Our testing also revealed a noteworthy surge in the production of both AAV and LV viral vectors.
Please refer to the Recombinant Insulin application page for a comprehensive collection of available application notes on insulin usage.
Your insulin is a powder. How do I dissolve it and what stock concentration do you recommend?
To dissolve the powder:
Suspend the insulin product in WFI or purified water.
Dissolve the insulin product by adjusting the pH to 3 with diluted HCl (0.1 or 0.01M, depending on the desired volume of growth medium). The insulin solution should not be held at pH 3 for more than one hour.
Readjust the pH to 7.4 with buffer or base. The solution becomes cloudy when passing through the isoelectric point of the insulin product, but becomes clear again as the pH of the solution reaches 7.
The solution should be sterile filtered using a low protein binding filter with a pore size of 0.2 μm. Avoid aeration and foaming during solubilisation and filtration, as this can lead to protein denaturation.
The recommended concentration of Recombinant Insulin in cell culture media is 1 – 20 mg/L, depending on cell type and specific application.
What is the storage temperature for your Recombinant Insulin?
To maintain the quality of Recombinant Insulin, store it at -20°C (+/-5°C) in its original container, shielding it from humidity and sunlight to prevent potential degradation and ensure compliance with the product specifications throughout its shelf-life.
For a total of 14 days during its shelf life, the Recombinant Insulin may be stored at refrigerator temperature (+2 to +8°C). During the shelf-life period, the product should not be thawed and refrozen more than five times. When dispensing the product for use, it may be handled and stored at temperatures of up to 25°C for up to 24 hours. Once dispensed, the product should be stored at +2 to +8°C until use.
These guidelines and restrictions are applicable from the time of shipment from Novo Nordisk Pharmatech and pertain to the original primary packaging container.
What is the stability of insulin following dilution?
When reconstituted in an aqueous solution following the guidelines in our document “Insulin Human AF Dilution Instructions”, the insulin solution can be stored at room temperature between +18°C and +22°C for a period of up to 2 days, or in a refrigerator at 5±3°C for a maximum of 23 days. This information is based on internal testing and should be considered as a guideline applicable specifically to aqueous solutions prepared according to our recommendations.
For alternative conditions, we recommend conducting an independent stability study.
What is the shelf life of your Recombinant Insulin?
Our Recombinant Insulin has a shelf life of 5 years from the date of manufacturing.
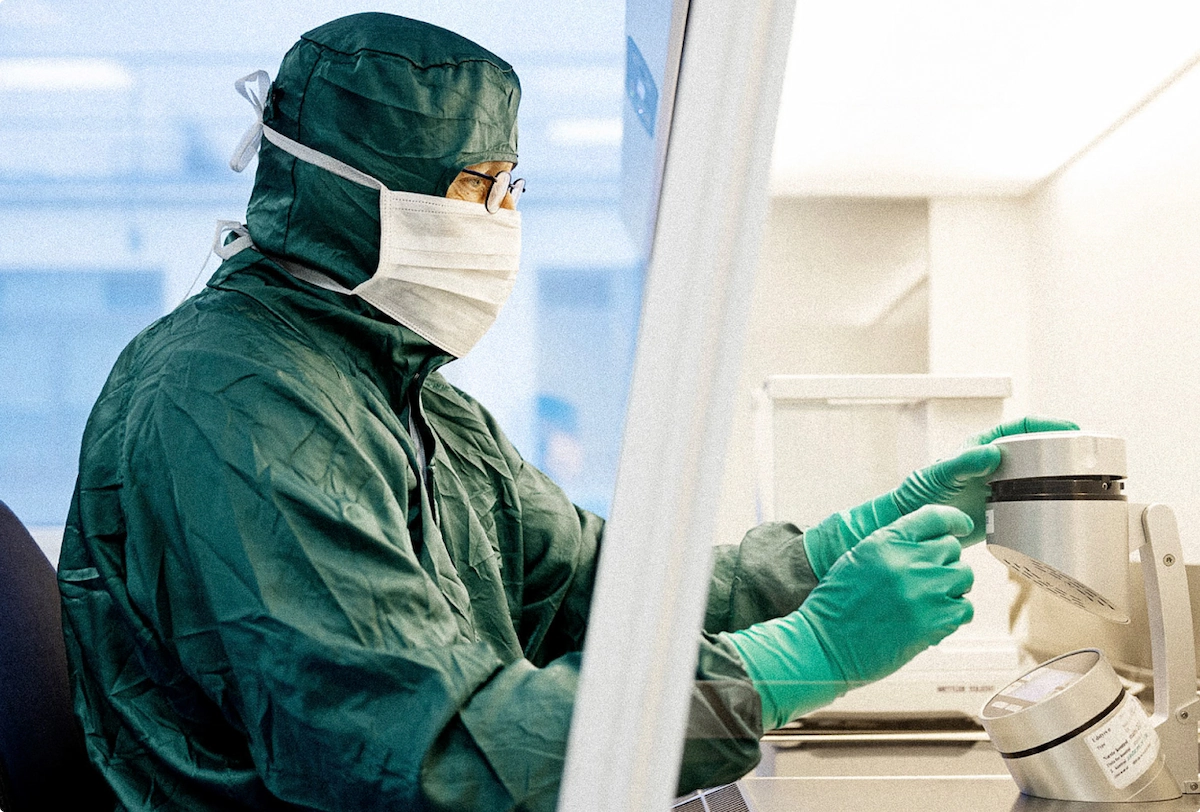
Where can I learn more?
For more information about our Recombinant Insulin products, please contact us or visit our Recombinant Insulin solution page.
Explore more about Recombinant Insulin
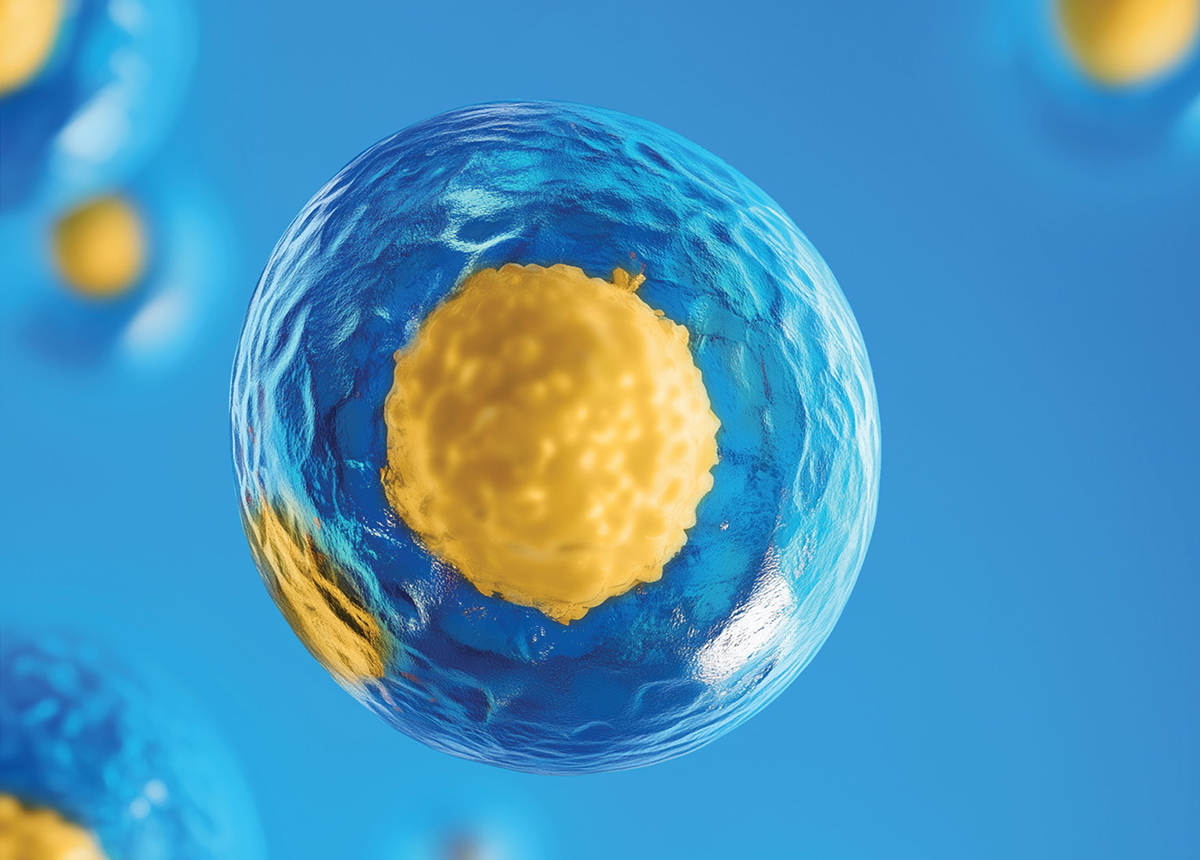
Insulin insights
Explore our collection of materials and case studies about Insulin Human AF and see how it improves cell culture and boosts protein production.
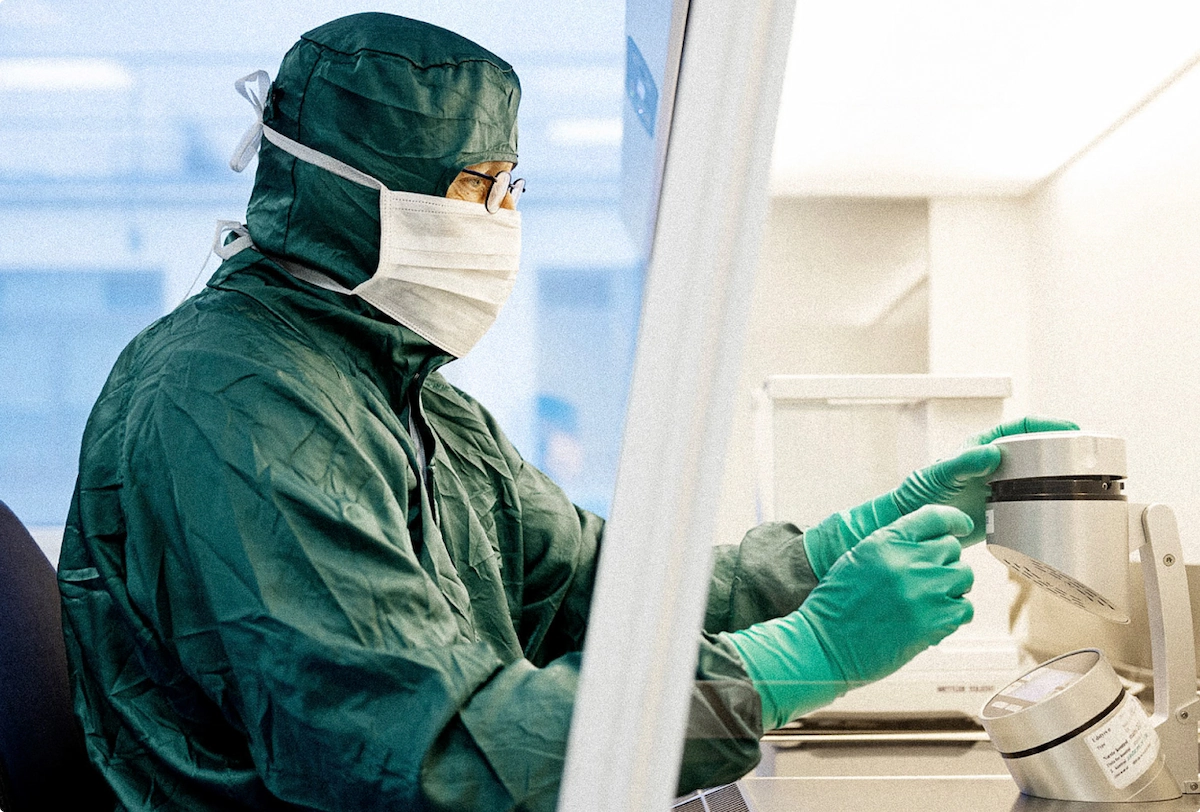
Recombinant Insulin
Scale-up production, optimise processes, and increase cellular products yields with our Recombinant Insulin that’s approved by regulatory bodies worldwide.
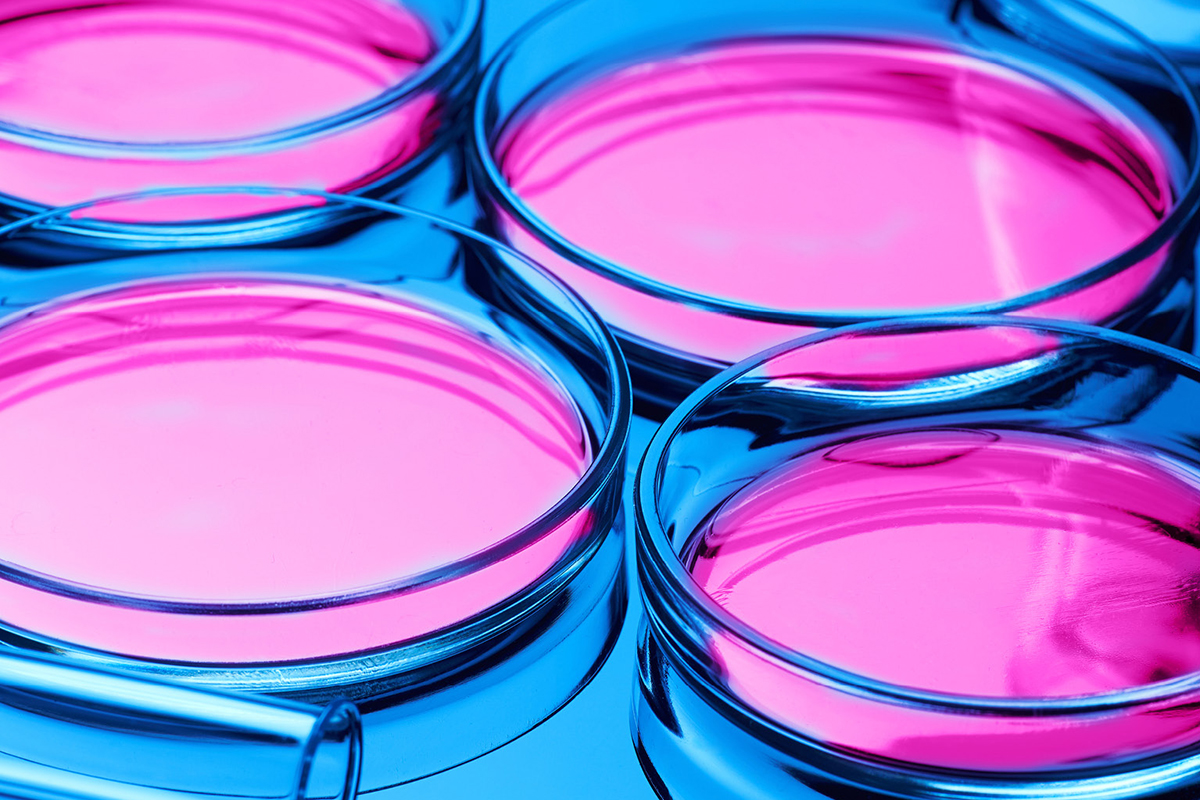
Insulin 10 reasons why
Improved cell culture performance and increased yield with Recombinant Insulin. High quality and consistent performance batch after batch. Read more
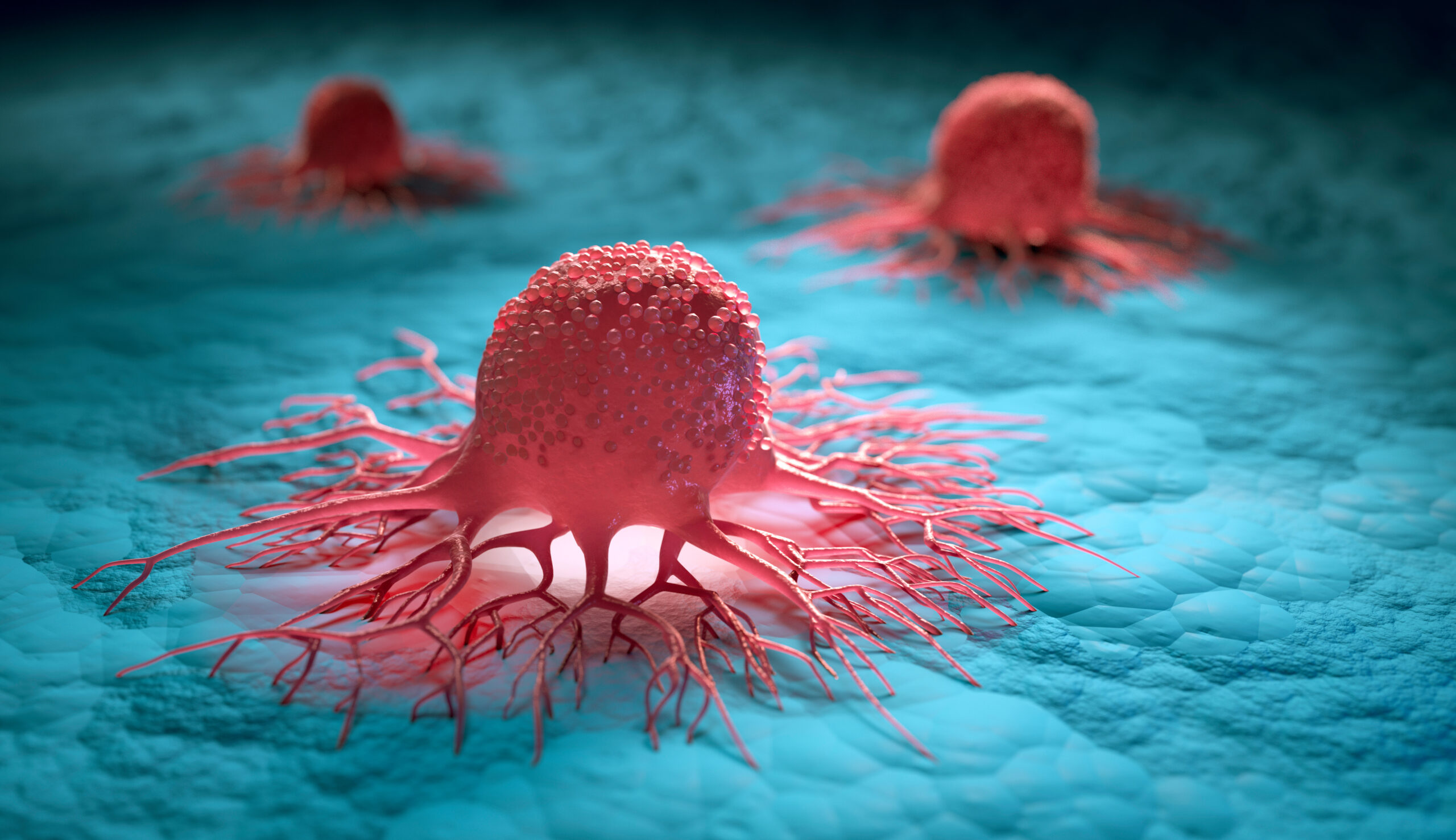
Insulin applications
Explore the many applications and learn how it can help support your formulations.